Surface Treatment
Our tailor-made solutions and products reveal the ingenuity in approach of the diverse applications for coating and inks industries.
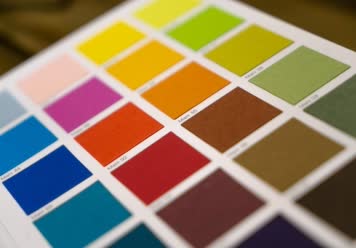
Our environmentally friendly polyurethanes, acrylic and natural
polymer technologies, with our oleochemical platform, offer us
a wide toolbox to support customers in their challenge.
With a strong focus on innovation, we provide performing and sustainable solutions in different fields.
Thanks to our consolidated expertise and our passion for collaboration, we supply a complete range of ingredients for the coating, inks & finishing industries as detailed hereinafter and, in detail:
Moreover, with a dedicated team of experts, we’re pleased to support our customers in the development of waterborne ink & digital ink for inkjet printing.
go to websiteBy combining the unique polymer beads technologies of Lamberti Spa (previously Supercolori, Italy) acquired in 2016 and Microbeads (Norway) acquired in 2020, Lamberti Group can offer the widest polymer beads portfolio in the market.
The range includes technologies under the brand names Decosphaera® (urethane beads) and Spheromers® (acrylic beads). The acrylic and urethane chemistries are complementary offering different advantages and solutions including both soft and hard beads.
The technologies include both extremely monosized particle size distribution and more Gaussian distribution covering a wide range of properties and end applications.
The unique pigmented Decosphaera® range offers design solutions like multicolour effects in addition to the highly transparent Decosphaera® and Spheromers®.
We’ve a very long experience into the Textile industry and our experts are able to developed ingredients for Textile Printing and Finishing markets.
Our experts are passionate to deliver leading and innovative solutions that can enhance performances and preserve resources of our planet.
go to websiteBased on Natural Polymers technology and renewable raw materials (Esacol®), we have developed a wide range of additives for cement and gypsum Dry Mix plasters and mortars.
For customers looking for ready mix products, we can offer the Esa-One® technology, a family of products based on the best combination of our additives for dry mix powders and wet systems.
go to websiteThe competitive advantage of our Lamberti solutions for Wet End Paper lies in the multilevel partnership with our Customers.
We develop and expand our value chain thanks to the transparent communication and reciprocal activities.
go to websiteWe could confidently say that we know the chemical formula of art. Innovative, experimental approach with a twist of creativity and passion in product development allowed us to produce, commercialize, and apply ready-to-use formulations that could be transformed into unique effects on the skin.
In our center of competences, where formulation chemistry and application skills are blended, we provide a full technical service to our customers in order to identify and develop taylor-made products.
We offer water-based ready-to-use products such as Base-Coat and Top-Coat, together with a wide range of other auxiliaries to develop your leather items in the various sectors: furniture, automotive, shoe-upper and leather goods.
go to websiteWe produces waterborne synthetic polymers: polyurethanes, PU-microBeads, acrylic resins and other chemical specialties which are the backbone of leather finishing formulation.
Our research & development and industrialization activities are guided by the logic of "performance improvement" approach and "sustainable" chemicals for leather finishing solutions. We are competent and organized to offer all customers who operate in this sector a specific support service connecting science and applicative solution.
go to website