- Innovation
- science
- sustainability
The Urea-Less Project
How to use less urea in textile printing to reduce environmental impact
When a "magic" product becomes a problem
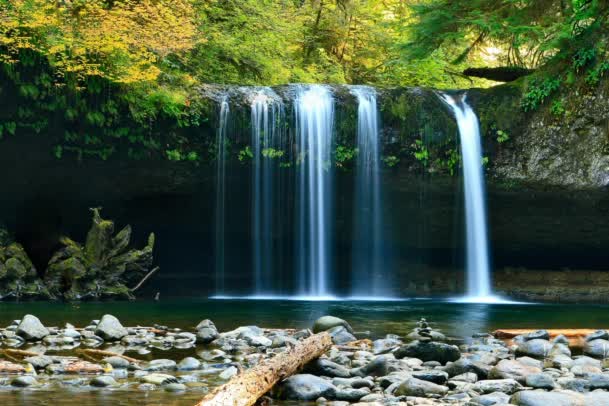
Urea is an essential component in textile printing with reactive dyes because it allows a good color rendering. Unfortunately its massive use generates an high concentration of nitrogen in the waste water: urea undergoes a first hydrolysis and subsequent oxidations and is found in the waste water in the form of ammonia, nitrites and nitrates. The presence of large concentrations of nitrogen can lead to eutrophication of the water. For this reason the european regulations impose important restrictions on its concentration in waste water.
The target of our research project was to reduce the quantity of urea used both in the printing pastes in traditional textile printing and in the liquors for the preparation of fabrics for printing ink jet, so as to reduce the urea and nitrogen content to be treated in the waste water treatment plants, with an undoubted benefit on the environmental impact and a lower incidence of costs for final operators.
Urea has been a fundamental component in the printing of reactive dyes since the 1960s because it helps the solubilization of dyes and consequently it favors the penetration inside the fiber.
The use of urea underwent an exponential growth when aside of the traditional printing it was introduced the digital printing. While in traditional printing, urea is inserted into the printing paste, in ink-jet it is used in the pre-treatment: the fabric, in its entire height, is completely pre-treated with a liquor containing urea even if the final print can be a simple flower or a pois dot. After steaming, the fabric is washed, releasing all the components of the pre-treatment liquor into the waste water, excluding the ink (reactive dye).
In both printing processes, we can consider urea a magical ingredient, which costs little and works very well, hence the difficulty in imagining a project to significantly reduce it and the difficulty for our customers to perceive urea as a problem. The legislative restrictions and the consequent increase in the wastewater treatment cost, combined with the growing sensitivity towards environmental problems have made the perception of the problem grow exponentially and pervasively from Brazil to Korea, from China to Italy but the adoption of solutions still is a slow and difficult process.
Up to now, we have focused on Ink-jet printing. Some customers have been more sensitive than others to our proposal. For many the issue remains essentially focused on the impact that the new proposal can have both on recipe costs and consequently on finished products.
The customers feedbacks are very positive although the transition from the laboratory phase to the industrial scale up , which is the real decisive test, is not always that immediate. Today we have introduce into the market the Compound Jet R/LU for digital printing and the Lamjet R / LU for traditional printing.
The design and implementation of the project was particularly difficult because it involved the replacing of a simple, cheap and very efficient product with a chemical component, soluble in water, nitrogen free , not dangerous for people or the environment. but which guaranteed the same performance and effectiveness of urea without increasing the production costs.
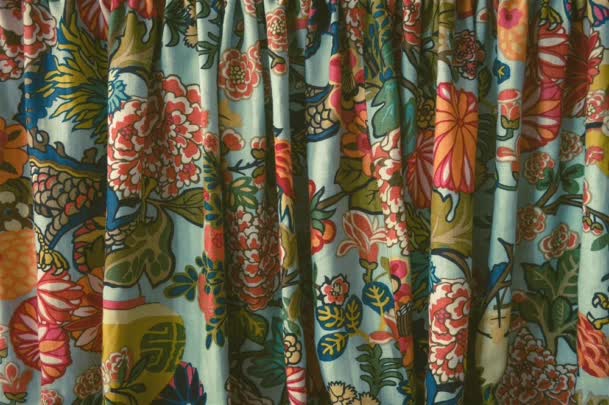
Thanks to our experience in developing formulations and to the input of our customers, we have been able to combine new molecules, synthesized in our technological laboratories, with traditional products, obtaining a reduction in the quantity of urea used in the process of about 40%. These data have been confirmed at industrial level.
For us, as researchers that was and remains a difficult project. We were certainly aware that a positive result would have had an important impact on the environment but we were facing with a a series of constraints and challenges that, at first, seemed insurmountable.
Now we are on the market and need to move forward: we must explore other raw materials and push our research into traditional printing.
As always it happens in research, the journey never ends.